+86-571-63780050
+86-18918137728
19941084290
Base Glass Composition
The base glass composition is critical for determining the thermal and mechanical properties of anti-deformation glass. Common types of base glass include:
A. Borosilicate Glass
- Key Components : Silicon dioxide (SiO₂), boron trioxide (B₂O₃).
- Properties :
- Low coefficient of thermal expansion (CTE), making it highly resistant to thermal shock.
- Excellent dimensional stability under temperature changes.
- Commonly used in laboratory glassware, cookware, and industrial applications.
- Applications : High-temperature environments like furnace windows, automotive headlights, and aerospace components.
B. Aluminosilicate Glass
- Key Components : Silicon dioxide (SiO₂), aluminum oxide (Al₂O₃).
- Properties :
- Higher mechanical strength and scratch resistance compared to standard soda-lime glass.
- Improved thermal stability due to the incorporation of alumina.
- Often chemically strengthened through ion exchange processes.
- Applications : Smartphones (e.g., Corning Gorilla Glass), architectural glazing, and protective screens.
C. Soda-Lime Glass (Modified)
- Key Components : Silicon dioxide (SiO₂), sodium oxide (Na₂O), calcium oxide (CaO).
- Modifications :
- Additives like magnesium oxide (MgO) or zinc oxide (ZnO) can improve thermal and mechanical performance.
- Tempering or laminating processes further enhance its resistance to deformation.
- Applications : Automotive windshields, windows, and general-purpose glazing.
Additives to Enhance Thermal Stability
Additives are incorporated into the glass matrix to reduce thermal expansion and improve resistance to high temperatures:
A. Boron Oxide (B₂O₃)
- Role : Reduces the CTE by disrupting the silica network structure.
- Effect : Enhances thermal shock resistance, making the glass ideal for applications involving rapid temperature changes.
B. Aluminum Oxide (Al₂O₃)
- Role : Strengthens the glass network and improves mechanical durability.
- Effect : Increases resistance to scratching, bending, and thermal stress.
C. Magnesium Oxide (MgO) and Zinc Oxide (ZnO)
- Role : Act as stabilizers to improve thermal and mechanical properties.
- Effect : Reduce brittleness and enhance toughness, especially in aluminosilicate glasses.
D. Lithium Oxide (Li₂O)
- Role : Used in chemically strengthened glasses to facilitate ion exchange.
- Effect : Improves surface compression and mechanical strength.
Surface Treatments and Coatings
Surface treatments and coatings are applied to further enhance the anti-deformation properties of the glass:
A. Chemical Strengthening (Ion Exchange)
- Process : Sodium ions (Na⁺) in the glass surface are replaced with larger potassium ions (K⁺) at high temperatures.
- Effect : Creates a compressive stress layer on the surface, significantly improving mechanical strength and resistance to deformation.
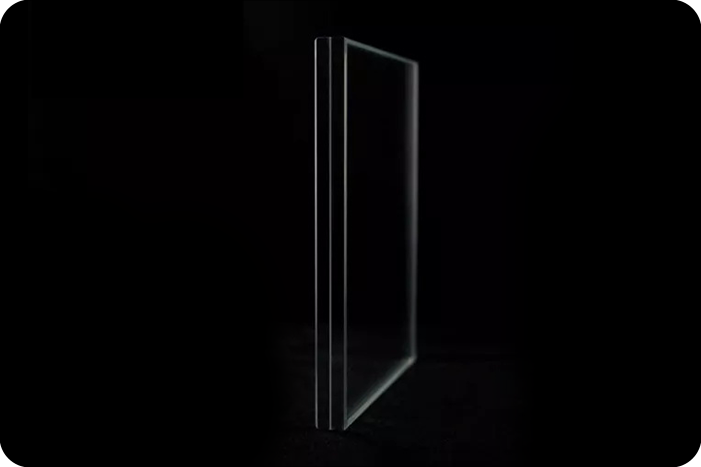
B. Thermal Tempering
- Process : The glass is heated to a high temperature and then rapidly cooled.
- Effect : Induces compressive stresses on the surface and tensile stresses in the core, enhancing strength and thermal shock resistance.
C. Anti-Reflective and Low-Emissivity Coatings
- Materials : Thin layers of metal oxides (e.g., tin oxide, titanium dioxide).
- Effect : Reduce light reflection and emissivity, improving optical clarity and thermal insulation.
Composite and Laminated Structures
In some cases, anti-deformation glass is combined with other materials to enhance its performance:
A. Laminated Glass
- Structure : Two or more layers of glass bonded with an interlayer (e.g., polyvinyl butyral, PVB).
- Effect : Improves impact resistance and prevents shattering, making it safer and more durable.
B. Hybrid Materials
- Structure : Glass combined with polymers or metals.
- Effect : Provides additional flexibility and strength, useful in foldable displays or flexible electronics.
Advanced Manufacturing Techniques
Advanced techniques are used to refine the material properties of anti-deformation glass:
A. Nanostructuring
- Process : Incorporates nanoparticles into the glass matrix.
- Effect : Enhances mechanical strength, thermal stability, and optical properties.
B. Controlled Cooling
- Process : Slow cooling (annealing) to relieve internal stresses.
- Effect : Reduces the risk of deformation or cracking during use.
Examples of Specialized Anti-Deformation Glasses
A. Pyrex (Borosilicate Glass)
- Composition : ~80% SiO₂, ~13% B₂O₃.
- Applications : Laboratory equipment, bakeware, and industrial components.
B. Corning Gorilla Glass (Aluminosilicate Glass)
- Composition : SiO₂, Al₂O₃, Na₂O, MgO.
- Applications : Smartphone screens, tablets, and other electronic devices.
C. Schott Robax (Transparent Ceramic Glass)
- Composition : Combination of glass and ceramic materials.
- Applications : Wood-burning stoves, fireplaces, and high-temperature viewing windows.